The Latest from Southwest Farm Press
horses grazing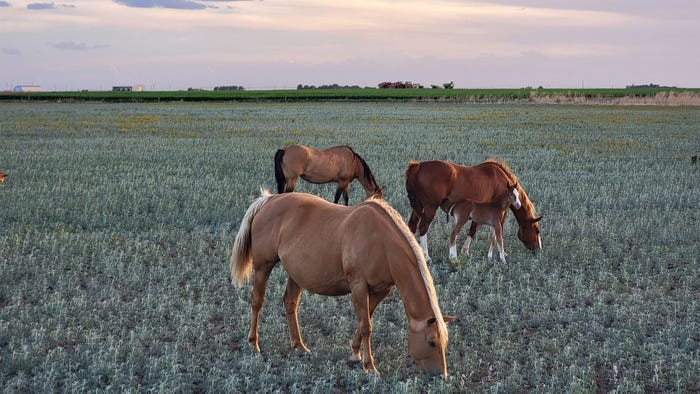
Animal Health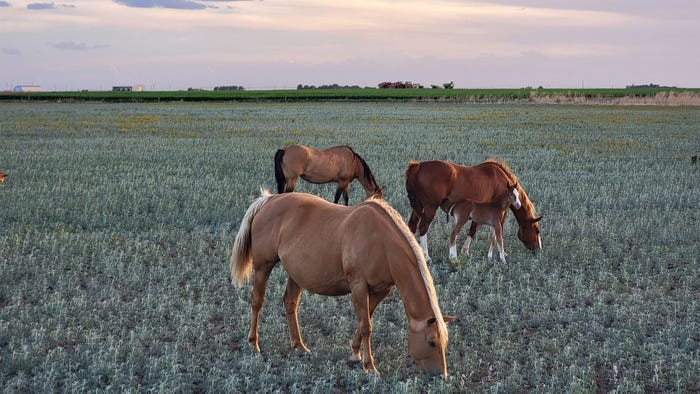
Texas boasts largest U.S. horse populationTexas boasts largest U.S. horse population
Survey reveals the economic impact of the horse industry in Texas. Land owned or leased for horse-related uses is estimated at 1.6 million acres or about 2.2 acres per horse.
Market Overview
Contract | Last | Change | High | Low | Open | Last Trade |
---|---|---|---|---|---|---|
Jul 24 Corn | 452 | unch — | 453 | 451.5 | 451.75 | 06:16 AM |
Jul 24 Oats | 356.75 | +5.75 | 356.75 | 352.25 | 352.25 | 05:06 AM |
May 24 Class III Milk | 18.25 | +0.07 | 18.28 | 18.25 | 18.28 | 04:21 AM |
Jul 24 Soybean | 1179 | -0.75 | 1181 | 1178 | 1179 | 06:17 AM |
Aug 24 Feeder Cattle | 258.3 | +2 | 258.8 | 254.25 | 256.425 | 06:04 PM |
May 24 Ethanol Futures | 2.161 | unch — | 2.161 | 2.161 | 2.161 | 09:38 PM |

Copyright © 2019. All market data is provided by Barchart Solutions.
Futures: at least 10 minute delayed. Information is provided ‘as is’ and solely for informational purposes, not for trading purposes or advice.
To see all exchange delays and terms of use, please see disclaimer.
All Southwest Farm Press
Subscribe to receive top agriculture news
Be informed daily with these free e-newsletters