The Latest from Southwest Farm Press
Smart farming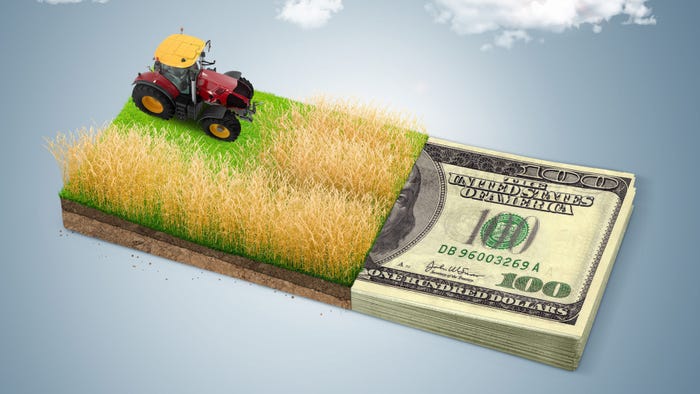
Farm Business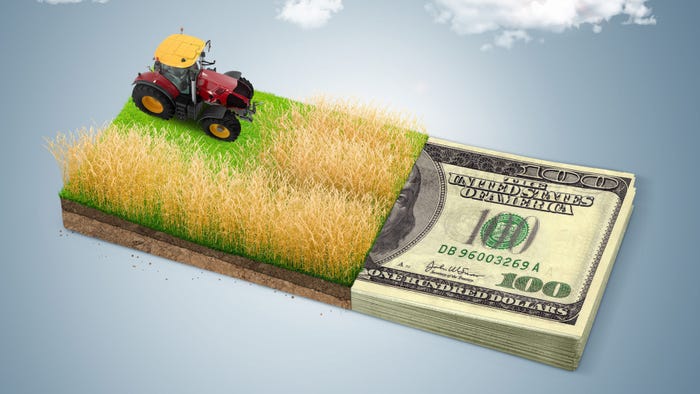
How can AI add value on the farm?How can AI add value on the farm?
AI has potential to analyze data, increase efficiency and improve accuracy when used in agriculture settings.
Market Overview
Contract | Last | Change | High | Low | Open | Last Trade |
---|---|---|---|---|---|---|
Jul 24 Corn | 453.5 | +1.5 | 454 | 450.25 | 451.75 | 04:58 PM |
Jul 24 Oats | 355.25 | +4.25 | 356.75 | 352.25 | 352.25 | 04:54 PM |
May 24 Class III Milk | 17.98 | -0.2 | 18.4 | 17.72 | 18.28 | 04:57 PM |
Jul 24 Soybean | 1178 | -1.75 | 1181 | 1172.5 | 1179 | 04:58 PM |
Aug 24 Feeder Cattle | 260.775 | +2.475 | 261.55 | 258.35 | 258.9 | 04:58 PM |
May 24 Ethanol Futures | 2.161 | unch — | 2.161 | 2.161 | 2.161 | 09:38 PM |

Copyright © 2019. All market data is provided by Barchart Solutions.
Futures: at least 10 minute delayed. Information is provided ‘as is’ and solely for informational purposes, not for trading purposes or advice.
To see all exchange delays and terms of use, please see disclaimer.
All Southwest Farm Press
Subscribe to receive top agriculture news
Be informed daily with these free e-newsletters